- April 5, 2024
Methane Mitigation Construction
Methane Mitigation Construction is a specialized field requiring a professionally trained team to implement the Mitigation. The requirements are outlined in the Methane Mitigation Design. Thus all Methane Mitigation Construction requires a Methane Mitigation Design, which a licensed Professional Engineer must prepare. Sway Features uses installation techniques for Mitigation Systems, which are non-standard procedures. Importantly noted, these systems commonly vary between projects and require certification and licensure. Sway Features is fully licensed and certified to construct Methane Mitigation Systems.
Methane Ventilation System Construction
Methane Mitigation Construction is a specialized field requiring a professionally trained team to implement the Mitigation requirements outlined in the Methane Mitigation Design. All Methane Mitigation Construction requires a Methane Mitigation Design, which a licensed Professional Engineer must prepare. The installation techniques for Mitigation Systems are non-standard procedures that commonly vary between projects and require certification and licensure. Sway Features is fully licensed and certified to construct Methane Mitigation Systems.
Furthermore, the dangers of improperly installing ventilation systems can lead to high concentrations of methane within structures. Which can cause health and safety issues for the public. Sway Features’ team sets the standard for installation procedures, and inspection approaches to ensure that every design is properly installed per the Methane Mitigation Engineer’s requirements.
Methane Barrier Construction
Additionally to the methane ventilation system, a common mitigation feature is the methane barrier. The methane barrier is a patent material performing below the slab of structures. It acts as a sealant for the foundation. This sealant creates an impenetrable membrane preventing methane breaches into structures. Which forwards methane vapors properly to the sub-slab ventilation system.
Therefore installation techniques of the Methane barriers require certification, including extensive training and an approval process. Regarding the complexity of methane barrier installations, this certification pertains to a few select contractors within the Southern California area.
Sway Features is an approved applicator of Methane Barriers, our crew ensures a properly efficient installation for all of our jobs

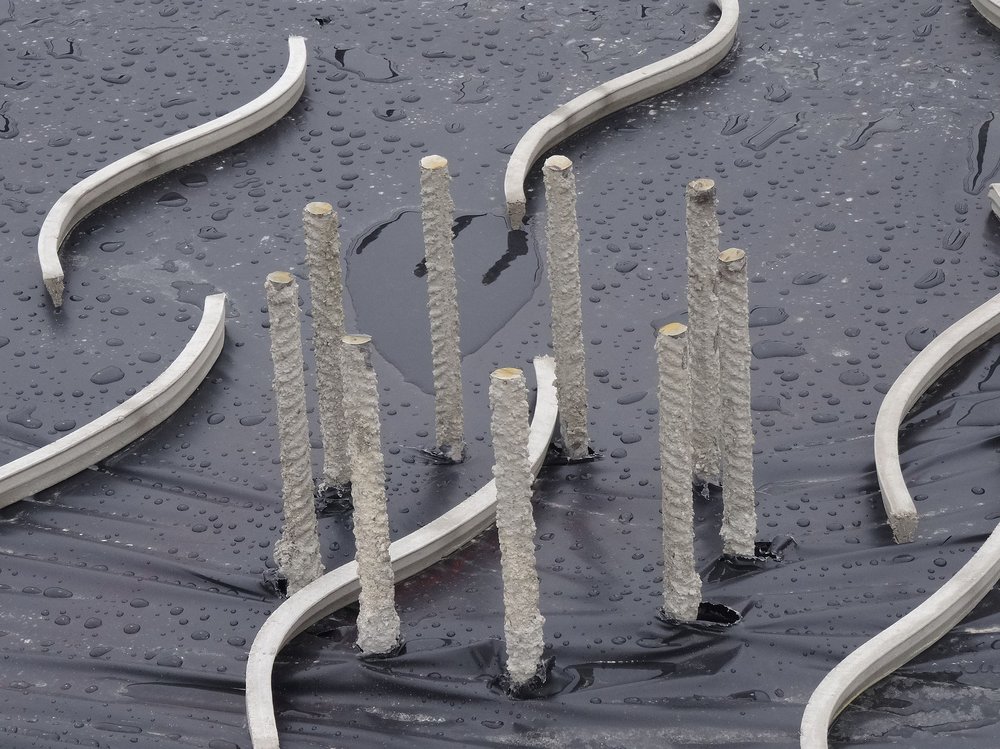
Methane Detection and Alarm Construction
In some cases for which the sub-surface conditions of the property contain high concentrations of methane, the Department of Building and Safety requires the installation of methane detectors and methane alarm systems within your building. Vitally, The Methane Detection system can monitor the concentrations of methane in the lowest space as well as the subsurface conditions. To detect if there are elevation of methane levels, it is a must that Methane Alarm System activation takes place. Local fire departments will get a notification.
The installation of Methane Sensors and Detectors requires expert-level electrical engineers and electricians. These comprehensive methane detectors and methane ventilation systems provide an additional safety measure for structures more prone to Methane Vapor Gas intrusion.
Install an effective and efficient system
In order to install an efficient system, there are Methane Mitigation Construction Requirements. A certified specialty methane mitigation contractor must conduct and execute these to install Methane barriers. It’s a must if the location of the project is in the methane zone or the methane buffer zone. Also if it includes a subterranean feature that methane easily migrates into. Construction must align with the LADBS Methane Mitigation requirements to ensure safety for the occupants.
The Methane barrier is one of the most critical components in Methane Mitigation Construction. A spray applies asphalt emulsions to create a Methane barrier. This material significantly increases the total cost of methane mitigation construction. Due to the highly sensitive application requires significant skill, knowledge, and equipment. But if properly applied, this material ensures a reliable methane barrier that will likely last longer.
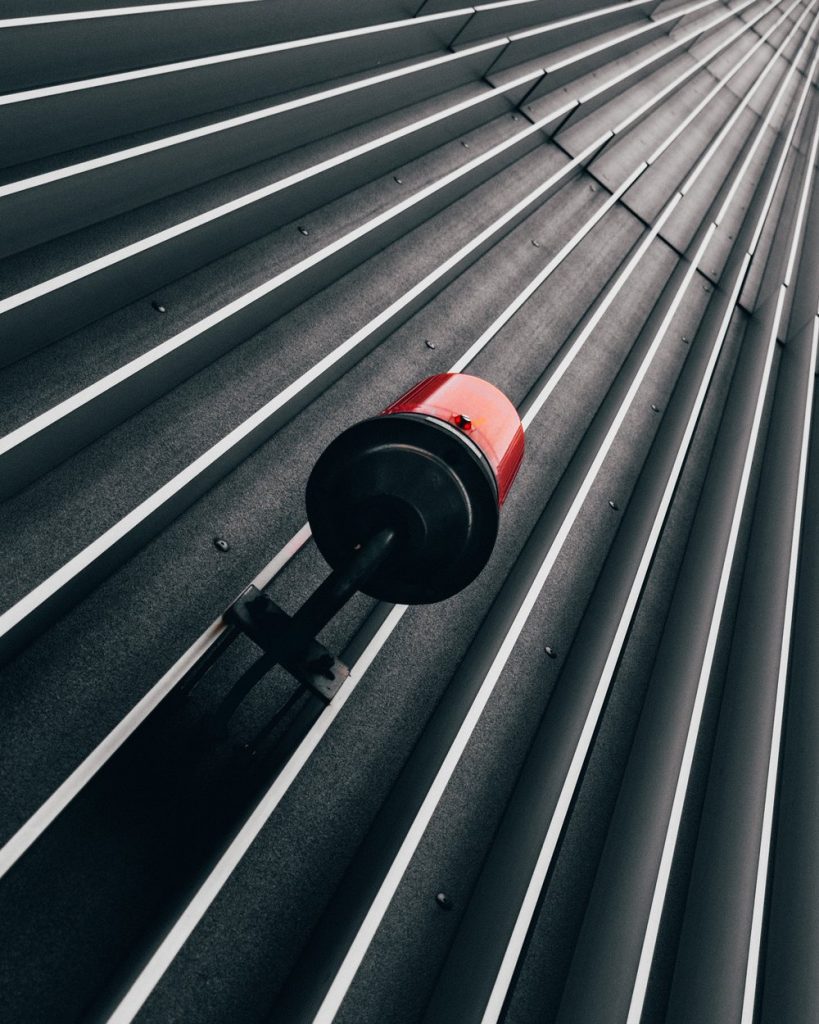
Sub Slab Vent Methane Vent and Vapor Barrier Installations
Aside from the methane barrier, the sub-slab vent system is another essential element in a Methane Mitigation Construction. The purpose of this system is for the depressurization in the subfloor. Which becomes necessary due to the accumulation of methane gas leading to high concentrations.
Meanwhile installing exhaust fans or blowers, a perforated pipe, and a gravel blanket below ground level will be successful. Consequently, despite these efforts, methane might still unnoticeably and steadily migrate into the building. So continuously monitoring methane density is vital. LADBS standards require the installation of Methane Alarms and Methane Sensors in the lowest area of the building. Therefore triggering can happen if certain methane density levels increase. If the Methane Mitigation Contractor has a license, they will test foundation seal security. Thus property owners and general contractors often take it upon themselves to prepare Methane mitigation systems to save on construction costs. It’s possible for specific projects, it’s a recommendation if the contractor is familiar with the Methane Mitigation construction process. This prep ensures that all required inspections and practices comply with the LADBS code.
One could save a lot of money with this approach. However, the scope of the project requires the installation of an actual Methane barrier. In that case, this aspect of the Methane Mitigation Construction Requirements must install by a certified applicator. They will observe the directions of the corresponding Methane barrier manufacturer. The manufacturer will only uphold the material and labor warranties if the approach is selected. In the case of any failures that’ll likely occur due to the sensitivity of methane mitigation construction, it may guarantee that there will be insurance coverage issues.
Why is my waterproof contractor installing my methane barriers?
New construction projects in the Los Angeles area often feature subterranean garages used for parking or basements used as livable spaces. When these project locations are in the methane zone, they will need unique Methane Mitigation Construction. It will require the implementation of methane programs. It is to ensure that the horizontal migration of methane into the structures is not taking place.
In these cases, Sway Features will install a special Methane barrier on the walls of the structures. Fortunately, for budget concerns, these walls require Waterproofing regardless. Often, the project manager for this type of construction will include a waterproofing budget. So long as your methane mitigation consultant correctly specifies the methane barrier used for the project, the membrane can also act as a waterproofing material.
Historical Background of Methane Barriers
Additionally, if a project has a location within the water table, the design and construction approach will lean toward a different direction. If this is the case, the consultant and contractor must ensure that the methane barrier can resist the hydrostatic pressure forces of the water from the ground. Methane barriers feature a boat-style in water table plans. Usually, installation is via a mat slab foundation and the waterproofing barrier construction.
What to know before hiring a Methane Mitigation Contractor!
The Methane Zone and Methane Buffer Zone only consist of a small ratio of the Los Angeles Department of Building and Safety’s Building Jurisdiction. These areas are on Historical Oil Wells or other methane-bearing sites. Other nearby building jurisdictions enforce the Methane Mitigation Code. This includes Long Beach, Orange County Fire Authority, LA County Environmental Programs Divisions, and more.
Thus it is vital to stay updated on the latest Methane Mitigation methods as a General Contractor, Building Owner, or Developer. Methane vapor or methane mitigation systems will, at minimum, include an underground ventilation system and a barrier. The Sub Slab Vent System is a design to reduce the subsurface pressure to prevent the migration of gasses into the buildings. The methane barrier prevents the spread of gasses into a structure by acting as a sealant at the slab level.
Often General Contractors that have inexperience with the Methane Vapor Mitigation trade are thrown off and believe that the matching rules specific in the Vapor Mitigation Design are unnecessary. Based on past events, including the explosion of the Ross Superstore, it is diligent and responsible for decreasing the risks linked with both Methane Gas Vapor Mitigation and the prevention of other contaminates as defined by DTSC that could cause Vapor migration issues.
Requesting Construction Bids for Vapor Mitigation Systems
This industry is new, so finding contractors may be tough in comparison to other trades. After the request to the bid, be sure to fully review the scope of work necessary for the methane mitigation construction bid.
Conversely, the vapor mitigation contractor must provide submittals that outline compliance with the terms marked in the Methane Mitigation Design. This is a crucial aspect of construction management. Methane Mitigation Contractors often implement lower quality barriers to win that project. It can cause problems for inspection, leading to high costs and delays. Therefore, to meet approval, the contractor must check and verify the Methane Mitigation design and the Construction bid for the Methane Mitigation System outline scope of work match markers on the LADBS-methane mitigation design.
LADBS Standard Plans used for Methane Mitigation Designs
Standard plans are prepared explicitly by the LADBS to provide generic instructions for engineers and contractors to refer to for methane mitigation systems. To save on costs, clients and architects can take on the design of the mitigation system using the standard plans as a source. The LADBS plan checker will often approve this design approach and accept the standard plans without added details.
Although, this is a more practical route during the design phase, having only the LADBS Methane Mitigation Standard Plans may not be signed off within your Plan Set. So, come time for construction, if there are no specific instructions for the contractor to build off of for the sub-slab, it may present harm. The system in the Methane Barrier or vent risers creates a mix-up, leading to cost points for constructing the Methane Mitigation System. Due to the LADBS strict Design, Construction, and Inspection Process, if your Standard Methane plans to make it through the Plan Check process, your LADBS Plan Checker will not accept the plans due to the lack of information available for inspection. Having no specific instruction will lead to lengthy added Methane Mitigation.
Design and Construction Permits and Inspection
The best action would be to hire a consultant to prepare a methane mitigation design specific to your project. Conversely, the consultant will outline everything a contractor and inspector need. Thus a consultant ensures that LADBS, plan to checks the project. So that your contractor is on the same page with your inspector regarding the scope of work for your project. Further, it will also help with funding, letting you get a Head start on the cost point of a Methane Mitigation System for your specific project.