- Published:
- Last Modified: April 5, 2024
Methane Mitigation Design
Methane Mitigation Systems is an application within known areas to ensure methane soil gas vapor will not intrude into buildings. Improper Methane Mitigation Designs can leave structures at risk of methane gas build up which may impose a violent hazard.
Thus Methane Mitigation rules are normally based on the closeness of current or old oil and gas production, landfills, or other areas stated by your building department. So the design process and rules can vary relative to the code rules for the city of which your property falls. Further, several building departments within Southern California have secure Methane Mitigation Design code requirements. This includes the Los Angeles Department of Building and Safety, Orange County Fire Authority, the County of Los Angeles Public Works Environmental Division, the City of Brea, the City of Montebello, and more.
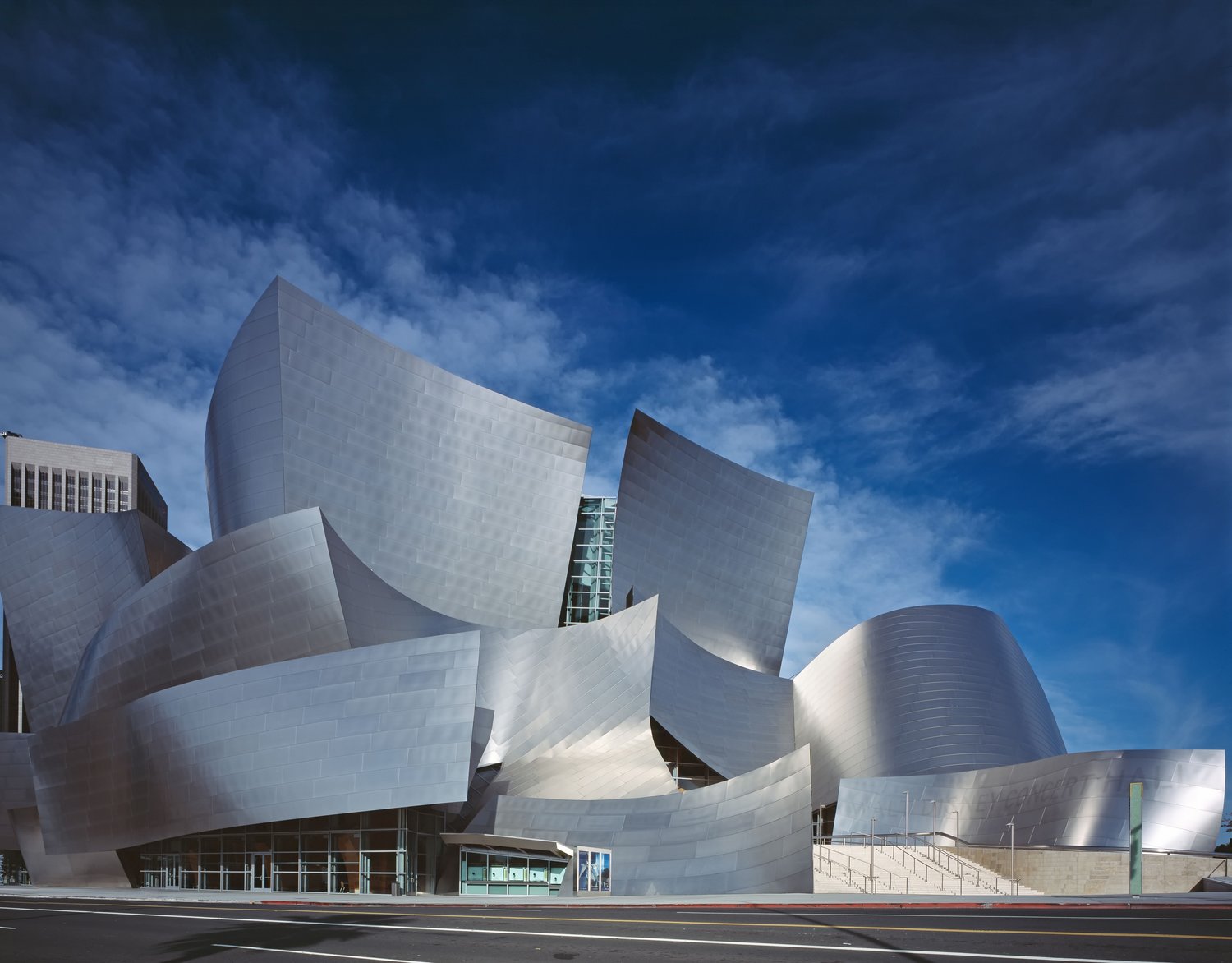
Los Angeles Building and Safety Methane Mitigation Requirements
Methane Mitigation System rules have been stated by the results of a Methane Test. So, Sway Features’ team of Engineers has experience with the latest design standards and building codes. Importantly, our team of environmental professionals uses design optimization methods to practically prevent the movement of methane gas into buildings.
Thus Sway Features has finesse in creating Methane Mitigation Systems for commercial buildings, multi-tenant residential projects, subterranean parking garages, underground vaults, basements, and single-family dwellings.
Furthermore, the City of Los Angeles has defined risky “Methane Zones” and “Methane Buffer Zones” based on current or old oil and gas production proximity. The Department of Building and Safety develops Methane Mitigation standards which must be in motion if construction falls within a Methane Zone or Buffer Zone.
Per Ordinance No. 175790 of the Los Angeles Municipal Code, buildings shall provide a methane mitigation system based on the appropriate Site Design Level. A Site Design level is based on the data reported during the Methane Test.
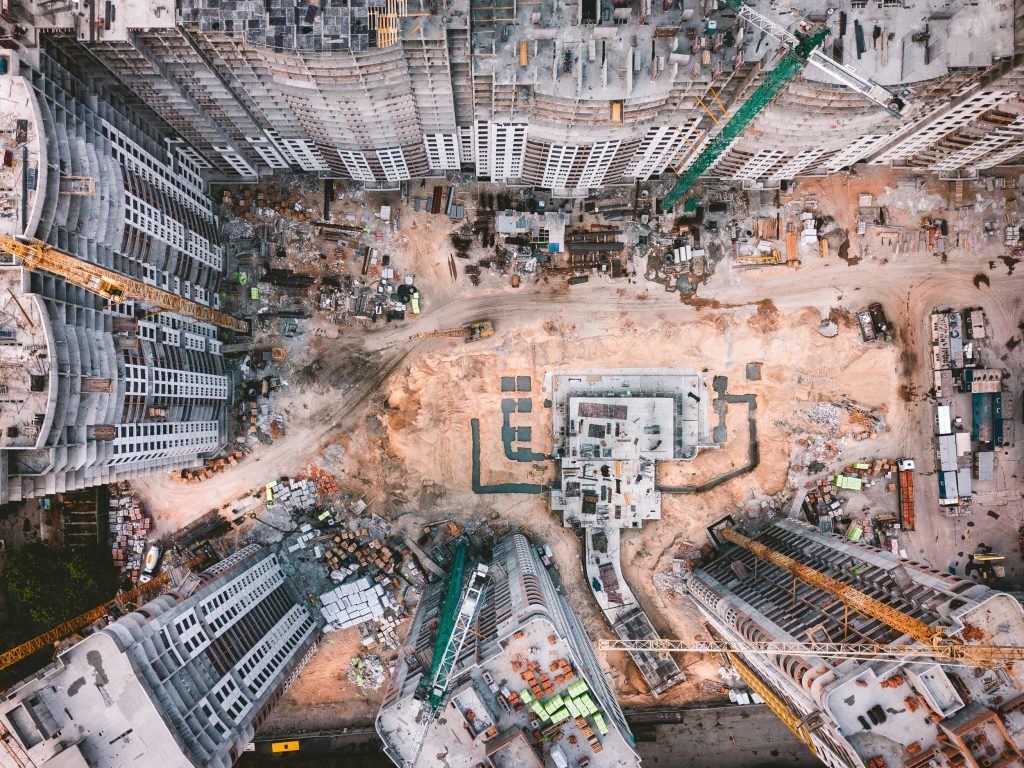
Methane Mitigation System Design Features
There are five LADBS Site Design Levels, each requiring different Methane Mitigation System design features. To start with, the Methane Mitigation system includes a trench dam and specifically designed methane extraction systems that are either “Passive” or “Active”. Then it also includes a ventilation system for the lowest space and a Methane Alarm system.
Trench Dam
To start with, Trench Dams are a design to prevent Methane Gas migration through trench backfills for subsurface utilities. The design approach includes handling material with low porous as a backfill substitute. Sway Features’ team implements proprietary backfill material composition; it is low cost and high performance.
Passive Methane Extraction Systems
Passive Methane Extraction Systems are a design to remove subsurface methane gas without mechanical influence. Therefore, a Passive System relies on the natural rising characteristics of methane to capture the accumulations of gas underground. Importantly, the gas naturally flows upwards into the atmosphere by the earth’s pressure.
Active Methane Extraction Systems
Active Methane Extraction Systems are composite of subsurface gas extraction fans. These mechanical Fans provide forced flow to migrate methane gas away from the sub-surface of a structure. Forced Flow provides induced pressure gradients in a region to prevent the accumulation of methane below the grade of a structure. Sway Features implements the latest Fan Sizing data to reduce material costs and complexity of Active Methane Extraction Systems.
Methane Ventilation Systems
Methane Ventilation Systems are a design to prevent the build-up of Methane Gas in the lowest space of a structure. Ventilation systems include Exhaust Fans and blowers to ensure that the Indoor Air quality of a structure is continuously safe for the occupants. Sway Features’ Engineers have experience with HVAC consultants who optimize the ventilation approach to ensure that a particular design satisfies the Methane Mitigation Code, and the ASHRAE Standard 62.2 for Indoor ventilation. Sway Features’ engineers collaborate with the HVAC consultant to ensure that the implementation of ventilation designs is efficient.
Methane Alarms and Sensors
Methane Sensors are to be put into the subsurface areas of a structure as well into the lowest space. These sensors are continuously monitoring concentrations of methane. If concentrations reach a threshold an active alarm system, it will trigger to notify occupants of the possible Methane Hazard.
Dewatering & Waterproofing in Methane Mitigation
Dewatering systems lower the groundwater table to a level below the bottom of a soil-gas ventilation system. Waterproofing barriers prevent groundwater from passing through a methane barrier. Sway Features specializes in designing dewatering systems and waterproofing barriers. This process involves communication with the architects and local building departments.
Methane Mitigation Construction
Sway Features offers methane mitigation construction services in all areas of California. Click Methane Mitigation Construction to learn more.
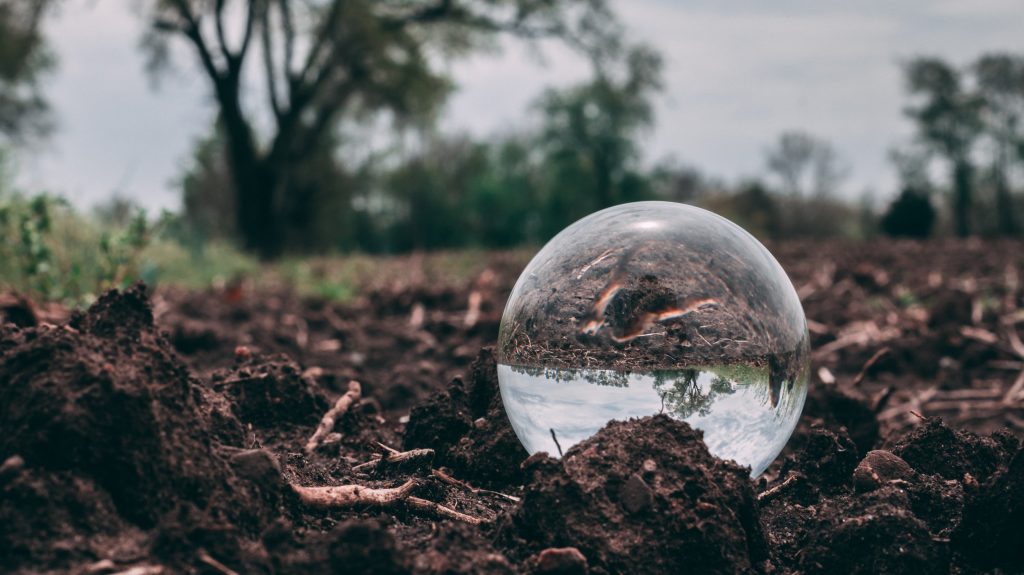
What is Methane Mitigation?
Methane Mitigation is a system installed to prevent and cancel methane vapor intrusion into a building’s foundation and concrete walls. Methane Mitigation is necessary for buildings situated in the Methane Zone or Methane Buffer Zone. These are zones categorized by the Los Angeles Department of Building and Safety (LADBS) as those with significant methane concentration levels due to abandoned oil wells and fields. ZIMAS can be used to verify if a project is in one of these zones and thus would need methane mitigation construction.
There is a higher risk of methane vapor intrusion if the project has a subterranean feature such as an underground garage or a basement. Methane gas vapor can quickly become explosive and asphyxiation inducing if continuously built up inside a structure. Naturally, highly concentrated methane gas from the surrounding soils would migrate into less potent spaces, usually inside a basement.
A methane mitigation plan that abides by the LADBS Methane Mitigation Standard Plans must be made to address this phenomenon. The LADBS Methane Mitigation Standard Plans have been around the time of the Ross Store explosion. Importantly, to prevent another damaging explosion from happening, the components in these reliable and verifiable methane mitigation plans are to implement in the methane mitigation design of all succeeding properties with a high risk of methane vapor intrusion.
Steps to Building a Methane Mitigation System
The Methane Mitigation Construction are an initiation by the methane testing within the soil using soil gas probes. The probes with vapor implants are to be placed at 5, 10, and 20 feet depths. Methane test results will use Levels 1 through 5 to categorize your project depending on recognizable methane concentration. The level will dictate the number of methane mitigation requirements to follow. Suppose results show that your property has the methane concentration level for a Level 5 property. In that case, there will be many more requirements to follow than a project at category Level 1.
Thus the methane mitigation requirements are outlined in the methane mitigation design and ultimately implement in the methane mitigation construction.
As you can see, methane testing must be done by a licensed methane testing agency listed on the LADBS database. A methane testing consultant with a license should prepare the methane soil gas report. If an unlicensed company completes methane Testing, LADBS may reject the test results leading to higher methane mitigation costs.
What are the Contents of a Methane Mitigation Design?
The methane mitigation design are part of a prep by an Engineer and will reflect the methane mitigation upon what category level the property is. For example a project classified as Level 5 usually requires all of the components in a methane mitigation construction. A complete methane barrier, “Passive” or “Active” methane extraction systems, a trench dam, a ventilation system for the lowest space, and a Methane Alarm system.
Passive Methane Extraction Systems work with the natural flow of highly concentrated gases such as methane into areas with less concentration. Without using any mechanical arrangements, subsurface methane gas capture and remove through these systems.
Moreover, active Methane Extraction Systems, on the other hand, use extraction fans that go below the ground surface to prevent methane gas vapor accumulation and force methane migration away from the subsurface of a building. Ultimately decreasing the mass diffusion rate of methane.
Ventilation systems such as the sub-slab vent system become necessary to decrease the mass diffusion rate of methane gas. It includes exhaust fans and blowers, a perforated pipe, and a gravel blanket. Implementing this system will also depressurize the subfloor from the methane gas buildup in the area.
Level 5 Methane Mitigation Projects
Projects categorized as Level 5, methane concentrations must monitor continuously. Methane Alarms and Methane Sensors are part of this for the purpose if concentrations reach a threshold, the alarm will trigger to warn occupants of the possible Methane Hazard.
So, these elements must be effectively and efficiently installed to ensure safety for the occupants. A Methane Mitigation Contractor with a license must be the consultant for methane mitigation construction ensuring all the LADBS standards meet satisfaction.
The methane mitigation design will change if the methane test result shows that your property is at a Level 1 Methane Buffer Zone area. It might not even require a methane mitigation construction at all. All projects are different, and the corresponding methane mitigation requirements will change; it is best to consult with the LADBS plan checker to evaluate to establish the final Methane Testing, Mitigation Design, and Methane Mitigation Construction requirements.
Key Components of Methane Mitigation Systems
The methane barrier is one of the key components of a methane mitigation system. It is an impermeable membrane that goes underneath the foundation and serves a seal for the concrete slab. Methane Barriers and Vapor Mitigation System have come a long way since the 1980s. The industry began due to the Ross store explosion.
Methane Mitigation engineers had to immediately come up with a solution after the destructive explosion. They thought of a methodology that included the construction and placing of a sealant beneath the foundation of a structure to prevent any penetration of harmful gases such as methane into the interior of a building.
Utilizing products that are already verifiable and have decades of proven field data seemed like the best option. Previously, waterproofing products had an establishment as effective and efficient. If these products can prevent water from seeping into structures, there is also potential of the prevention of methane vapor intrusion in these products.
A licensed LADBS testing testing agency tested some of these already existing membranes as methane barriers. Through the methane tests conduct, it was a confirmation that spray-asphalt emulsion waterproofing products decrease the mass diffusion rate of methane. Additionally, when verifying this, methane consultants and the LADBS develop specifications for methane barriers. Rules are useful to determine the most appropriate membrane for specific projects.
Evolution of Vapor Mitigation Systems
Methane Mitigation Systems are still continuously evolving, expanding, and optimizing. Initially, there were only one or two methane barriers that were at utilization. This was for several decades until recently when various Methane barriers are introducing to the lineup of products used in mitigating methane intrusion into structures.
In the past, the crew would spray-applicate asphalt emulsion into the barrier. The manufacturer offering this grew very quickly, ultimately having handfuls of approved spray-application Methane barriers. Methane barriers are useful simply to prevent the diffusion of methane through a surface. So several materials can meet this requirement. Modern companies introduce new methods for this. Therefore some companies introduce spraying onto a geotextile surface to allow for a base material to be useful.
Another significant change in the industry is one that doesn’t require a spray application. Some of these products are sheet or film membranes, and built-up or laminate membranes. Other methane mitigation contractors use peel-and-stick products consisting of rubber, bitumen, bentonite clay, polyethylene, and plastic sheet compositions. Although these products have their own advantages, they each have their own disadvantages. Peel-and-stick materials typically cost less, require less skilled labor, and have no curing time. Since they are prefabricated, they have controlled thickness in every single application. One significant disadvantage of peel-and-stick products is their moisture sensitivity. There is a high risk of debonding or membrane peeling.
The more common spray-applied asphalt emulsion requires skilled labor, curing time, and equipment which all increase the cost. However, the result is a more reliable and stable system that will typically last longer.
Methane Mitigation Designs Requirement Explained
Methane Mitigation or a Vapor Mitigation Designs are becoming a key element of the design and construction phase for all projects. The necessity of Methane Mitigation or a Vapor Mitigation Systems stems from environmental contamination concerns. So, one requirement by local building jurisdictions is the intent to prevent explosive gases migrating into structures. Another rule from the Department of Toxic and Substances Control’s (DTSC) approach to reduce toxic vapor intrusion into the interior space of structures.
If Design requirements specify that a Methane or Vapor Mitigation System must be part of the construction. Then a Design that includes the specifications of the Vapor Mitigation system must be available for the contractor that will be finishing the work.
Thus the Vapor Mitigation Design will specify the sub-slab depressurization system also known as the sub-slab vent system. It will also include vapor probe monitoring programs along with vapor or Methane Barrier details.
Methane Mitigation Design Details
Further design details may vary relative to the responsible Methane Vapor Mitigation Consultant. Generally, based on the code rules for both Methane Mitigation and the EPA’s DTSC Vapor Mitigation Advisory, the design will include these details the sub-slab vent system and methane or vapor barrier.
During the construction, the Methane Vapor mitigation system will have an inspection by a special inspector. This rule is by local building jurisdictions, or the manufacturer themselves to provide the relative warranty for the work that’s been provided.
Often, for lower-budget projects, developers may want to save on cost by not having a Mitigation design readily available. Although this surely will save on cost during the design phase of the project, this is not a recommended process for a Mitigation system. The Methane mitigation scope will slip in construction if no design in the plan set was made during bidding.
Additionally, if the methane mitigation design are not part of the plan set, then General Contactor can’t understand the rules. The Methane Mitigation and Vapor mitigation requirements are a recent addition to projects. It is common for General contractors to not be aware of the construction practices. It is urged for mitigation systems to prep for the Methane Mitigation Construction Bid and vapor mitigation design.